شیوه اول تشخیص خرابی در زمان وقوع یا به اختصار تشخیص خرابی (Defect detection) است. رویکردی که در آن تلاش میشود با استفاده از دادههای ثبت شده از گذشته فرایند و خرابیهای تشخیص داده شده و ثبت شده، تشخیص لحظهای خرابی صورت بگیرد.
نرم افزار تشخیص خودکار خرابی تجهیزات
تشخیص خودکار خرابی تجهیزات از روی سیگنالهای پایش وضعیت
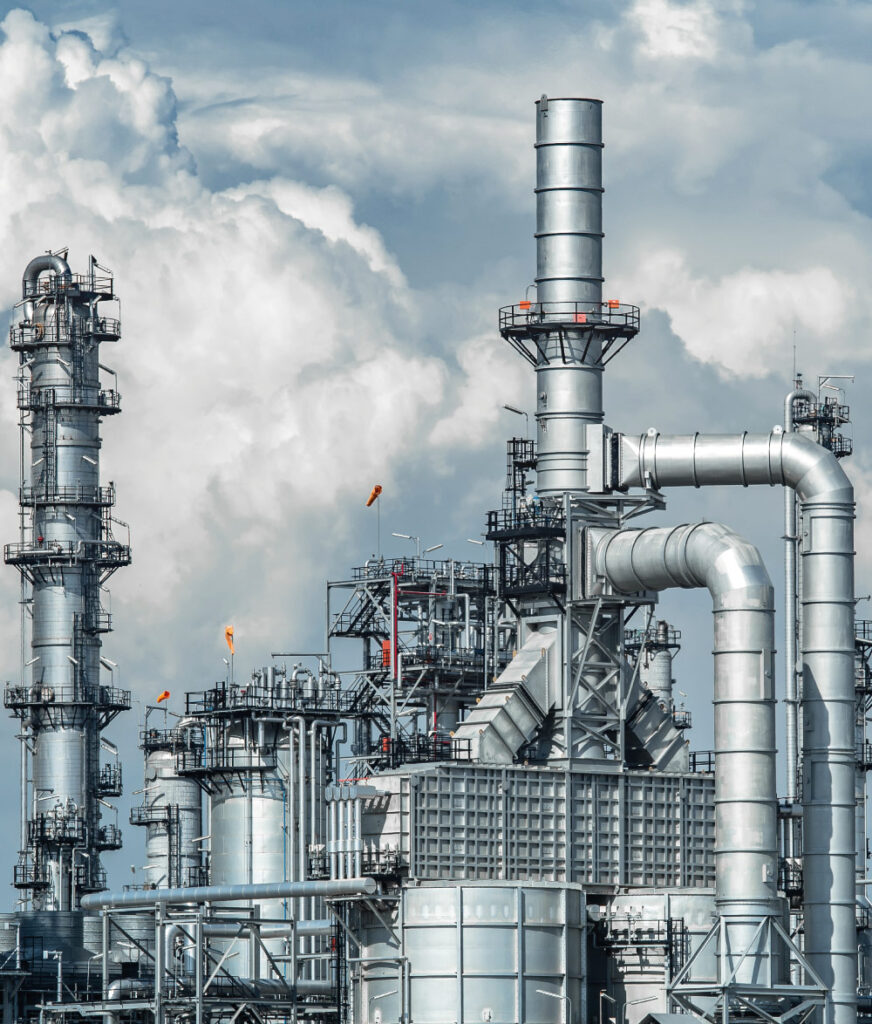
پیاده سازی سیستم تشخیص خودکار خرابی تجهیزات
در این گروه از پروژهها، هدف تشخیص خرابی یا نقص درون تجهیزات یا قطعات صنعتی و غیرصنعتی است. در حالی که، با استفاده از اکتساب اطلاعات مناسب از جنس سیگنال (مانند سیگنالهای لرزش، دما و صوت) فرایند تشخیص عیب به صورت خودکار صورت گرفته و از این طریق دقت و سرعت تشخیص عیب و خرابیهای احتمالی افزایش یابد. در مسائلی از این دست، به سه شیوه مختلف با خرابی و تشخیص آن برخورد میشود:
- تشخیص خرابی در زمان وقوع
- تشخیص خرابی پیش از وقوع
- برآورد مدت زمان کارکرد تجهیز بدون وقوع خرابی
تشخیص خرابی پیش از وقوع
در رویکرد دوم تلاش بر این است که تشخیص زودتر از زمان وقوع صورت بگیرد. این رویکرد تشخیص خرابی به اختصار پیشگویی خرابی (Defect diagnosis) نامیده میشود.
برآورد مدت زمان کارکرد بدون وقوع خرابی
در رویکرد سوم هدف برآورد مدت زمانی است که یک تجهیز یا جزء میتواند بدون وقوع خرابی کار کند. به عبارت دیگر، در این رویکرد که پیشبینی عمر مفید باقی مانده (Remaining useful time forecasting) نامیده میشود، تلاش میشود با مشاهده الگوهای مشخصی که پیش از وقوع خرابیها و به مرور زمان ایجاد میشوند، زمان احتمالی کار مفید یک تجهیز برآورد شود.
نرم افزار تشخیص خودکار خرابی تجهیزات که توسط شرکت دانش بنیان فن آوران گیتی افروز با مشارکت جمعی از متخصصان صنایع طراحی و توسعه داده شده است، از طریق بکارگیری روش ها و مفاهیم گوناگون دانش داده (Data science) و پردازش سیگنال، ابزاری هوشمند برای تشخیص خودکار خرابی تجهیزات، پیش بینی خرابی تجهیزات و پیش بینی عمر مفید باقیمانده قطعات است.
سیگنال هایی با ماهیت های مختلف همچون دما که اصطلاحا سیگنال های پایش وضعیت گفته می شوند، به عنوان ورودی اصلی و داده های اولیه جهت تصمیم گیری هوشمند و خودکار در نرم افزار تشخیص خودکار خرابی تجهیزات هستند. این سیگنال ها امکان بیان وضعیت سیستم یا تجهیز مورد بررسی را فراهم مینمایند.
کارکرد نرم افزار تشخیص خودکار خرابی تجهیزات
یک ماشین برشکاری بزرگ را در یک کارخانه تولید قطعات اتومبیل در نظر بگیرید. این ماشین از قطعات گوناگونی تشکیل شده است. یکی از قطعاتی که در معرض تنش و فشارهای زیادی قرار دارد، بلبرینگ است. به صورت سنتی، اپراتورهای این ماشینها از طریق گوش کردن صدای کار بلبرینگ احتمال وقوع خرابی احتمالی در آن را تشخیص میدهند.
این اقدام با توجه به وجود صداهای مختلف در محیط و احتمال اشتباه کاربر داری ریسک خطای بالایی خواهد بود. در مقابل، با نصب چندین سنسور صدا و لرزش در نزدیکی این قطعه و ثبت مقادیر این سیگنالها در طول فرایند کار قطعه، میتوان الگوی کار این قطعه را به دست آورد.
